Every time I crack my code book I see something I overlooked on the first pass. This morning was no different as I thumbed through the Roof Assembly – Chapter 9 – of the IRC 2009.
Before the 2009 IRC was published the only section that specifically addressed Sidewall Flashing (R905.2.8.4 in the 2006 IRC) said “Flashing against a vertical sidewall shall be by the step-flashing method.” Not a whole lot of detail there. Around where I work in southern New England that meant 5 in. x 7 in. mill finish aluminum cards bent with 2 1/2 in. wall and roof legs. I can’t count the number of times I’ve been called out to fix a roof leak problem that traced back to these puny step flashings.
Hopefully inspectors start enforcing the revised 2009 IRC section (R905.2.8.3) that calls for step flashings with wall and roof legs of 4 in. The extra 1 1/2 in. may not seem like a lot but when you consider that several manufactured sidings require that their product be kept off the roofing surface by 1 in. to 2 in., we need tall wall legs.
I still consider 4 in. legs inadequate and prefer to see a minimum of 5 in. on the wall and 5 in. on the roof. I start with 10 in. square flashing cards made of colored aluminum or copper and gang-bend nice crisp corners on a break. The nice thing about colored metal or copper is that the 1 in. to 2 in. exposed portion doesn’t cause you to squint when the sun reflects off as it will with mill finish aluminum.
And one other notable part of the the Sidewall Flashing section. “At the end of the vertical sidewall the step flashing shall be turned out in a manner that directs water away from the wall and onto the roof and/or gutter.” Wow – they codefied kick out flashings! This is a major major step in keeping water out of walls.
RELATED STORIES
- Kickout Flashing: How to Flash Troublesome Roof-to-Wall Intersections
- Bigger Flashing Solves a Persistent Problem
Fine Homebuilding Recommended Products
Fine Homebuilding receives a commission for items purchased through links on this site, including Amazon Associates and other affiliate advertising programs.
Reliable Crimp Connectors
Affordable IR Camera
8067 All-Weather Flashing Tape
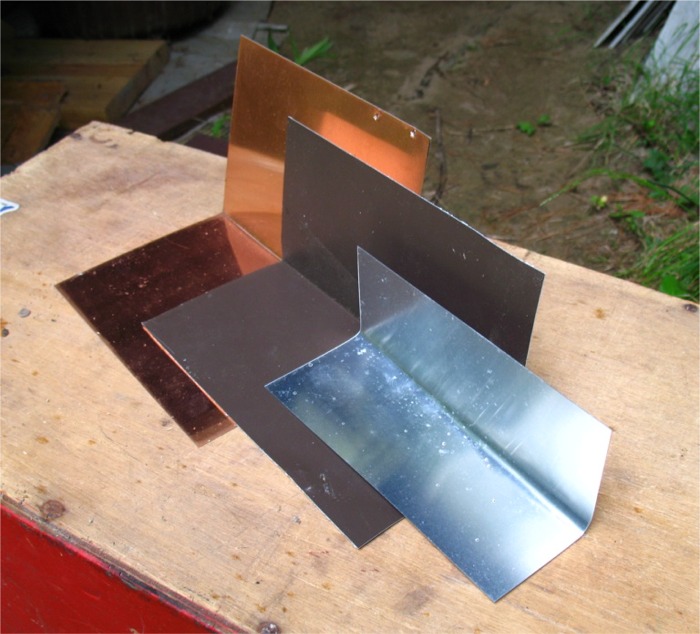
5x7 flashing cards don't cut it with the 2009 IRC. The wall and roof legs need to be at least 4 in. (middle flashing). But bigger is better - think 5 in. or more on the wall and roof.
View Comments
Sounds great. Now if I can only get the roofers to use the step flashing in the first place. To many times I have seen the roofers install the 30 lb. felt (ok) and then install the ice shield on the roof and then up the side wall (great). And then nothing, the siding goes on next. What? I say, no step flashing.? The roofer will say. No, that's what the ice shield is for.
I don't know but am I missing something? I don't get it.
With all this bs about contractors being licensed, there should be some basic testing in their field of trade. At least they should have a basic knowledge and understand of the job that they will be performing.
By implication, most stack flashings and attic vents have inadequate flashing surfaces and need to be a couple inches wider.
I agree with amazingrace what good is licensing if the contractor doesn't know the proper way of doing jobs.
The ice barrier degrades if left exposed to the elements.Read the label on the packaging.
In the past I have used 7"x7" flats bent to bent to 3 1/2" and 3 1/2" 90 degree. In my mind the new code is good and what Mike said is better. Thanks for the news
Whenever I'm called in to fix a leak it seems it always goes back to the flashing, particulary where the roofing shingles meet the cedar shakes, most times the cedar sits right on the asphalt, thereby wicking up the water. the cedar will rot and with only 2-3 inches of flashing going up the wall it will not handle a major downpour.
Follow-up to Creebomb's comment -
You're right, when siding is in direct contact with the roofing, you're asking for problems. There are code requirements, industry association technical information and product manufacturer instructions that all call for an airspace between the bottom course of siding and horizontal surfaces.
For me the space serves multiple functions. It's a good view point for flashing inspection; it prevents the wicking you noted - so the siding and paint/stain finishes last longer; it lets air flow freely so things that get wet can dry out; and it minimizes the chance debris will collect and foster decay.
And for those opposed to seeing mill finish aluminum - install a counterflashing strip of color-coated aluminum or choose another flashing metal (copper, lead, stainless).