How to Frame an I-Joist Roof
Engineered rafters are lighter, straighter, and often have more room for insulation than dimensional lumber.
There are many choices for roof framing: dimensional lumber, trusses, or engineered lumber such as laminated veneer lumber (LVL) and I-joists. All have advantages and drawbacks. On a recent project, an accessory dwelling behind an in-town bungalow, I was tasked with building a 16-ft. clear-span monoslope roof with a soaring cathedral ceiling on the underside. The logical choice was to use 14-in. I-joist rafters.
Advantages of I-joists
I-joists are great for roofs because of their consistent dimensions. And because they’re very straight, they create a dead-flat ceiling. I’ve had 2x12s range from 11-1/8 in. to 11-5/8 in. in the same delivery, which can cause waviness that shows up on the finished ceiling or the roof, likely both. LVL or LSL (laminated strand lumber) are also options, but they are more expensive and heavier than I-joists.
I-joists come in longer lengths than readily available dimensional lumber, which is great for roof spans. They also come in many depths and flange widths to accommodate snow loads and design considerations. Their extra depth means they can meet insulation requirements for even the coldest parts of the country with less-expensive fibrous insulation rather than foam.
For this project, we needed stock longer than 16 ft. In my area right now, dimensional lumber longer than 16 ft. is a special order with a very long lead time, but I was able to get 18-ft., 14-in.-deep I-joists in just a few days through a local lumberyard. Most good lumberyards have someone who can help with I-joist engineering and design, and manufacturers have approved installation methods for common overhangs and ridges, as well as hip and valley details.
Lay out the roof
Rafters are spaced 16 in. on center and positioned 1-3/4 in. away from the edge of the wall plate at the ridge to allow for a continuous LVL that transfers the roof load around the large south-facing windows.
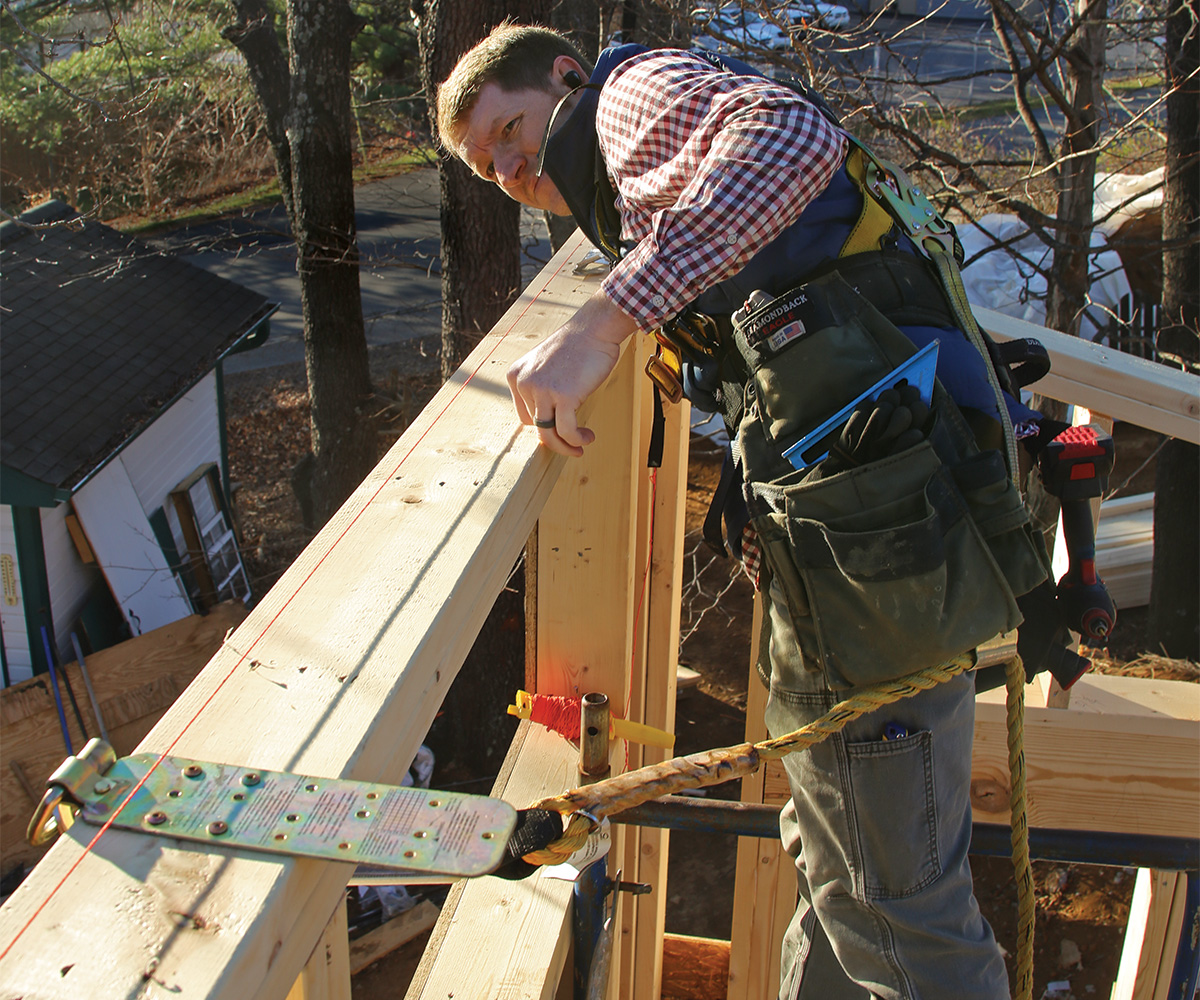
Prep the rafters
The rafters are cut and prepped on the ground on sawhorses before they’re lifted onto the roof. They should be stored banded together and lifted from both ends to prevent damage.
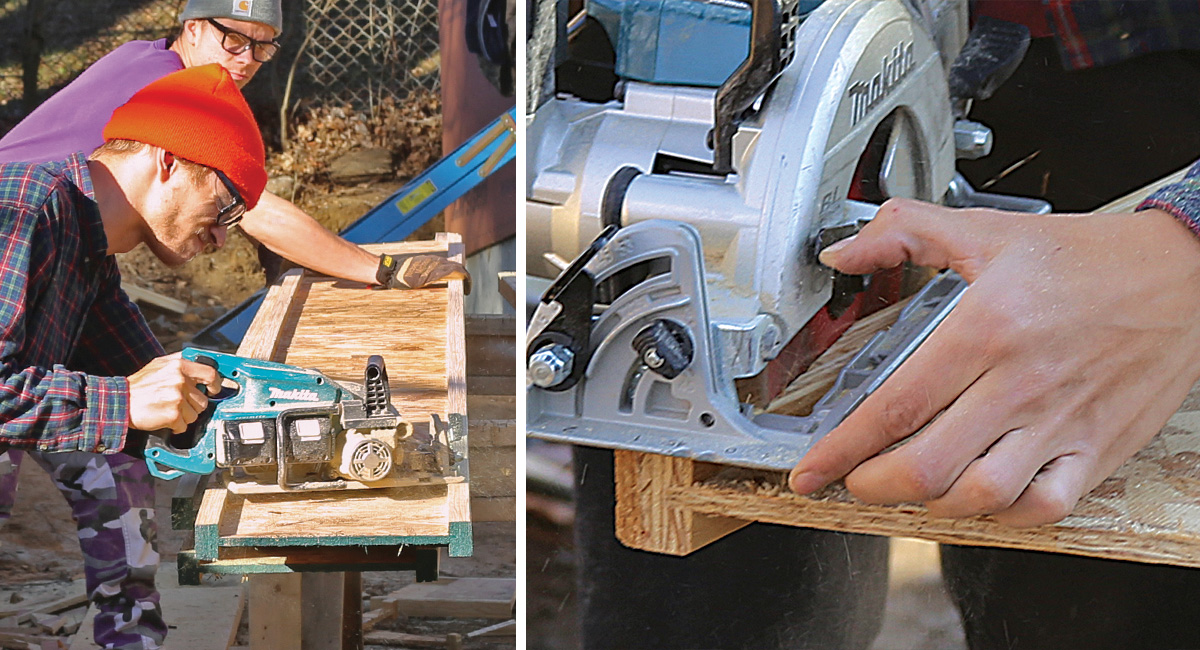
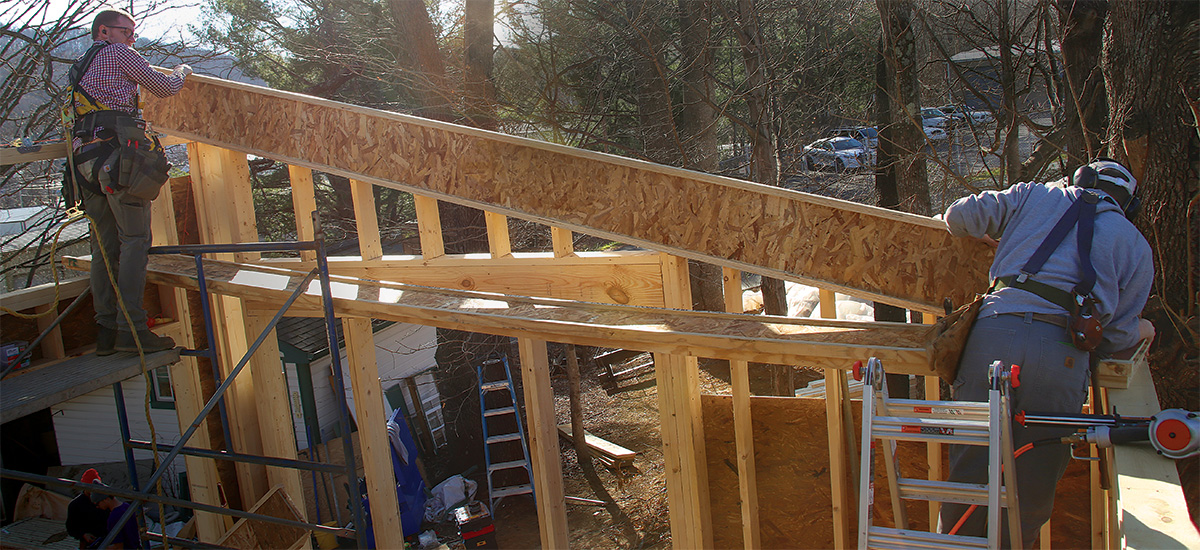
Approaching eaves and ridges
I-joist roofs have specific details for eave and ridge connections, and you have to follow the details provided by the specific manufacturer. Generally, there are several ways to deal with the bird’s mouths. The first is to avoid them completely with beveled top plates on the exterior walls. This works well if you are building with 2×4 walls, but not 2×6 walls; job-site tablesaws can’t rip a full-width bevel on a 2×6. You can bevel a 2×6 using a sled with a lunchbox planer, but it takes forever. I know—I’ve tried it.
Another option is to hang the rafters from a rim board with an adjustable face-mount hanger like Simpson’s LSSR. If you use this hanger, you have to pad out the web of the I-joist with 3-in.-wide pieces of plywood or OSB of a thickness that matches the width of the flanges. I attached the ridge end of my rafters with Simpson VPA Variable-Pitch Connectors (about $8 each), which can accommodate roof pitches from 3:12 to 12:12.
In order to create an uninterrupted taped-sheathing air barrier, we cut the “seat” portion of a bird’s mouth on the lower end of the joists but then trimmed them off flush with the wall framing. We installed the overhang later. To help the roof resist uplift, there are Simpson H2.5AZ connectors on every rafter on the inside. The I-joist webs are padded out for this connection.
Set the rafters
While a crew of two cuts and preps rafters, two other workers start nailing rafters in place, starting with the second rafter. The first and the last rafters that form the gable ends will be nailed in place later.
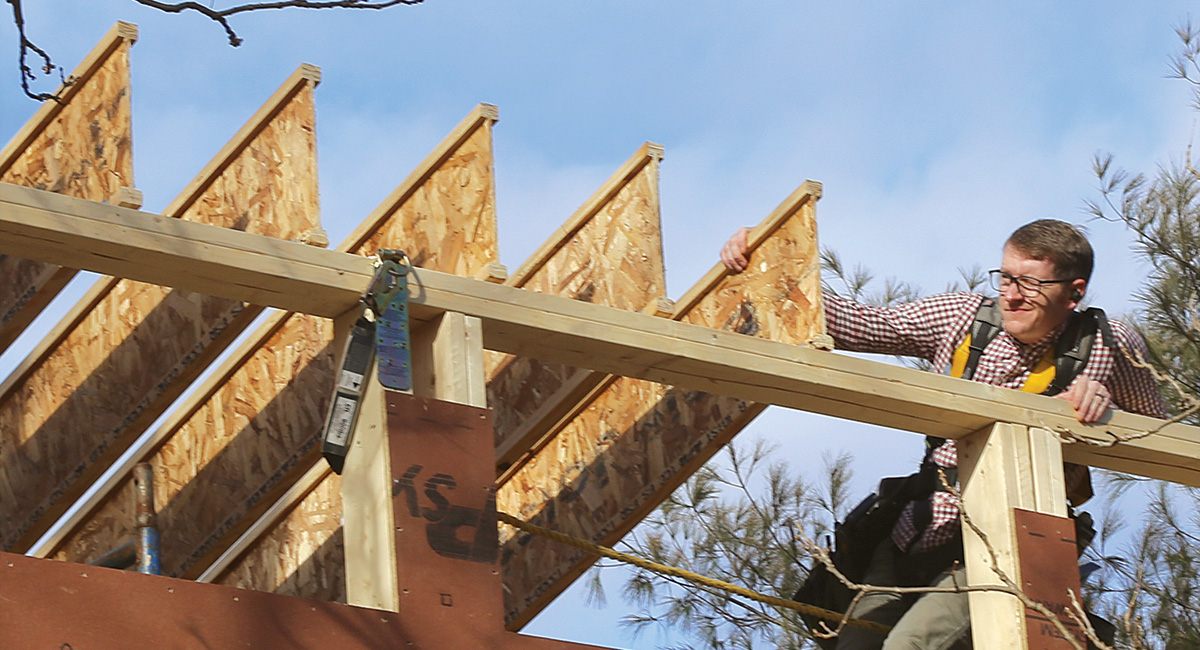
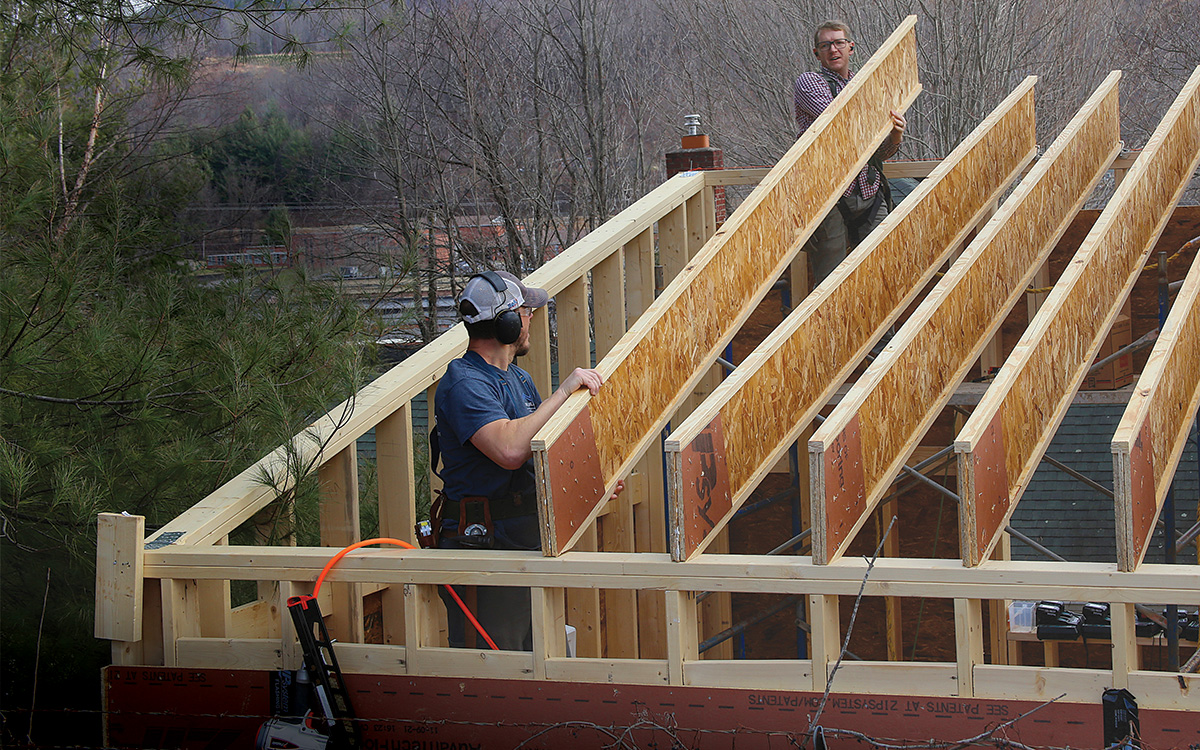
Sheathe the roof
The roof and the tops of the walls are sheathed together. Here, the top course was left off of the wall sheathing so that the crew could tie the wall sheathing into the roof system for greater uplift resistance in high winds.
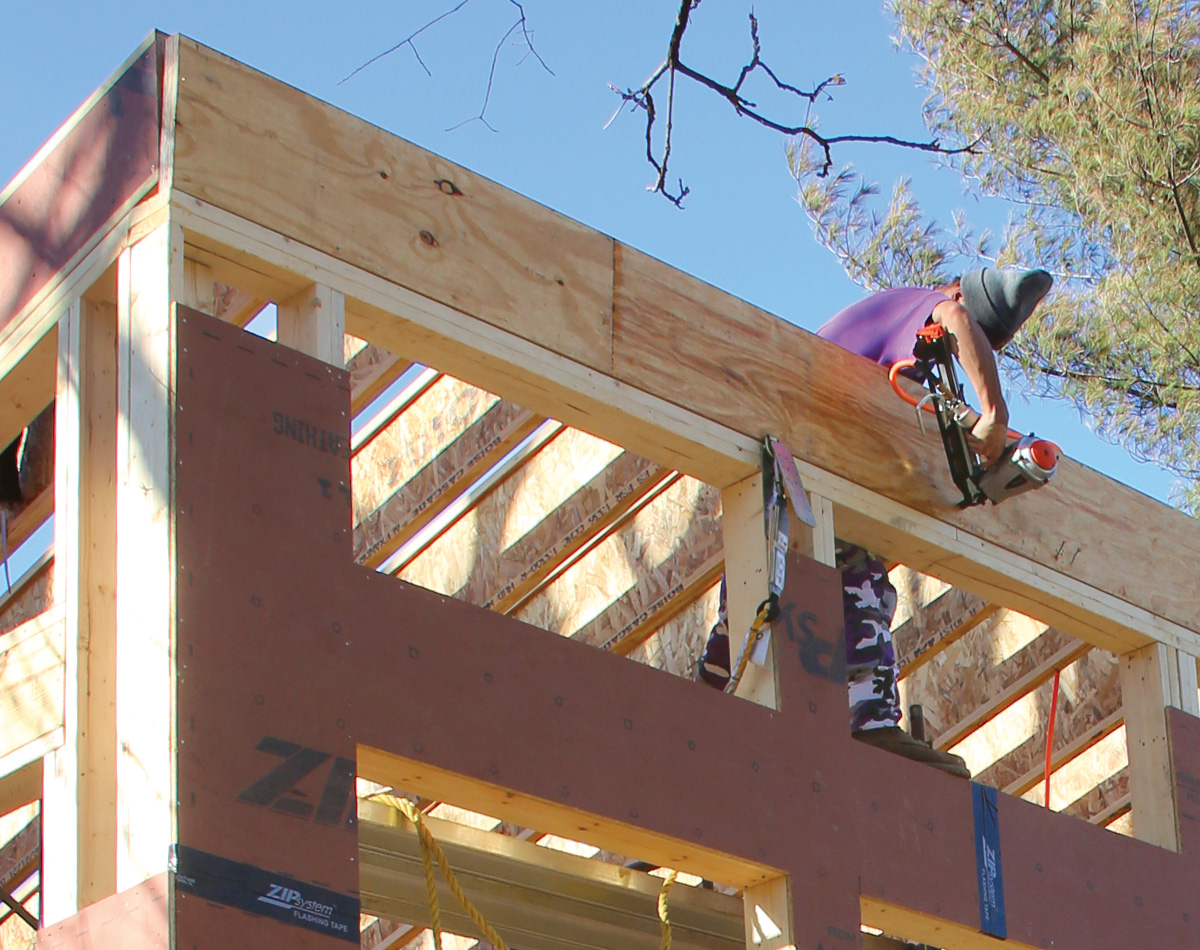
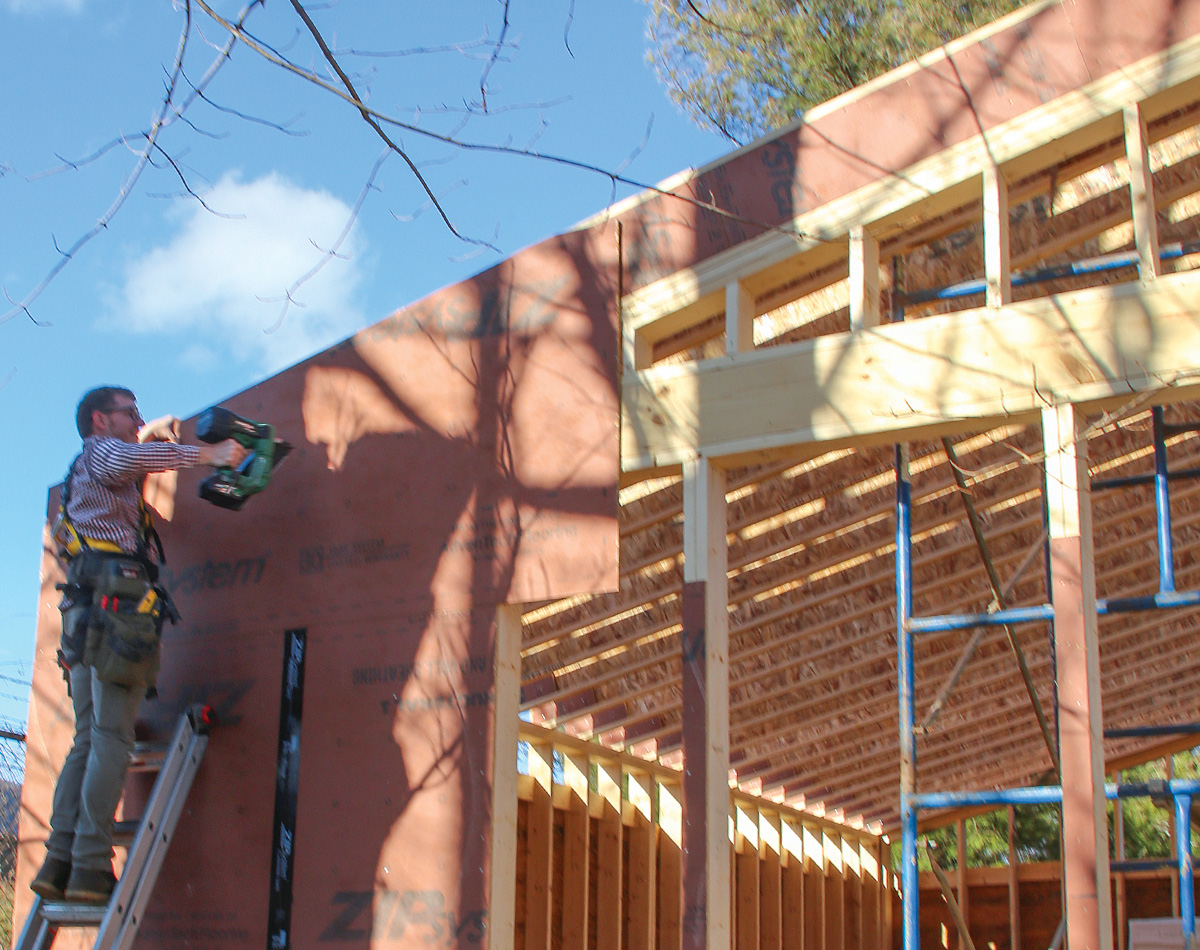
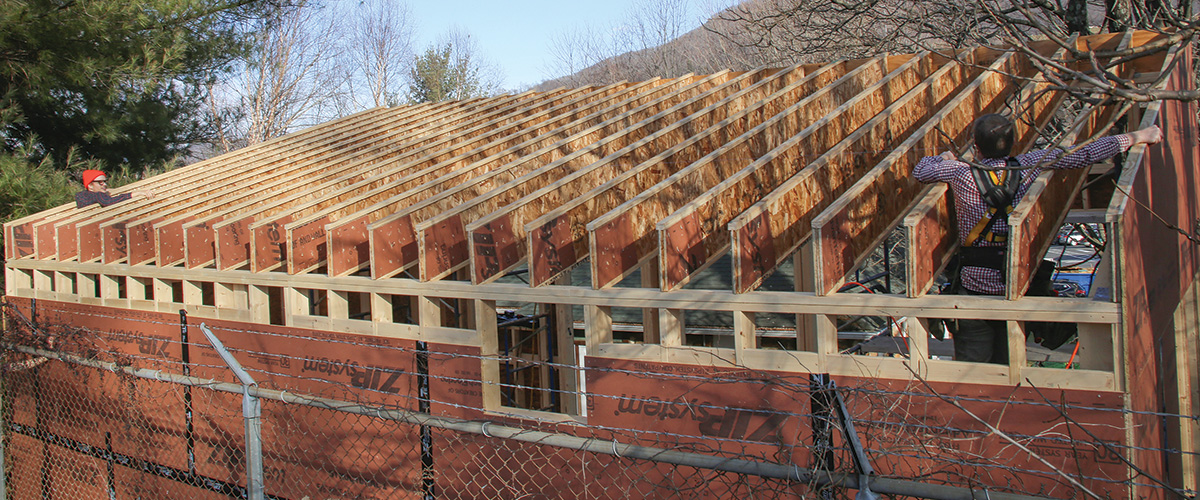
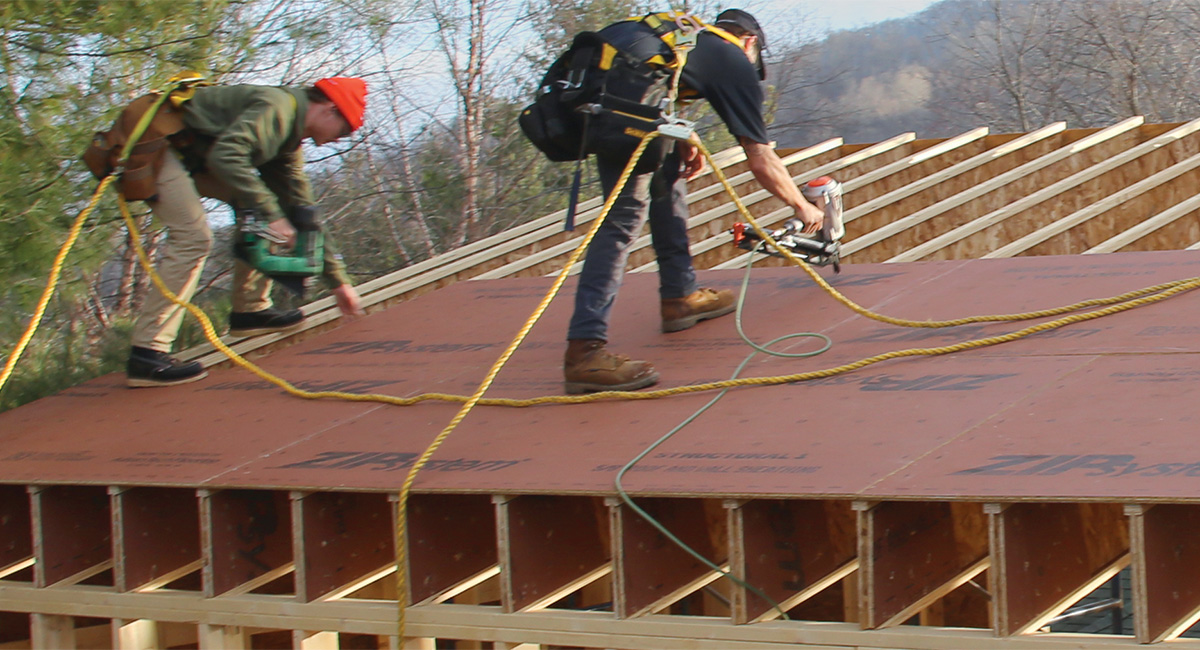
Details for blocking and venting
To prevent the rafters from rolling over under load, I used a manufacturer detail with blocking between each rafter on the low end of the roof using LSL rim board. (The blocking is also the attachment point for the applied rafter tails that will be installed later.) I waited to install this blocking until sheathing the roof and taping the seams so that I’d have a dry place for priming and painting exterior trim on rainy days. If I had to do it again, I would install the blocking before the roof sheathing, because fitting the blocking tight to the rafters is more difficult with the sheathing in place.
Creating a cathedral ceiling with an air space for venting is easy with I-joists. We used the top flange of the I-joist as a mounting point for 3/4-in. XPS foam. The space above the foam is the vent channel, and there’s still enough room for R-38 fiberglass insulation below the foam, the code minimum for a sloping ceiling in my climate zone.
The XPS foam was nailed to the underside of the flange using a roofing nailer, and the edges were sealed with canned spray from. On the lower end we drilled a series of 3/4-in. holes through the sheathing to connect the vent space to the outside. On the ridge end we cut holes in every bay with a router.
Plan for venting
With I-joist roof framing you can attach rigid insulation to the bottom of the top flange to create a space for a vented roof. The ridge and eave are treated differently when it comes to venting.
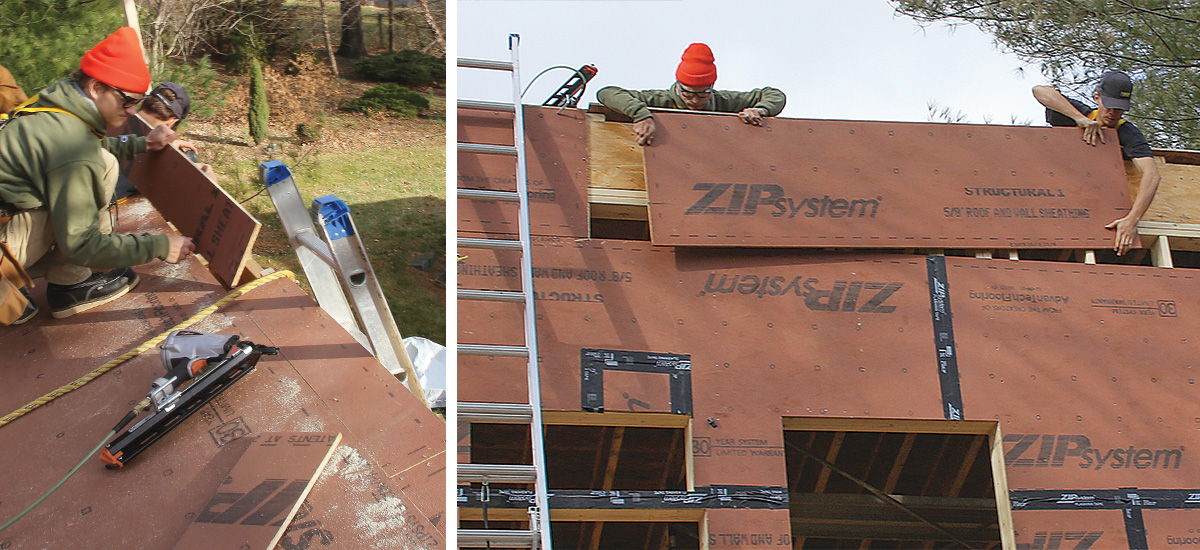
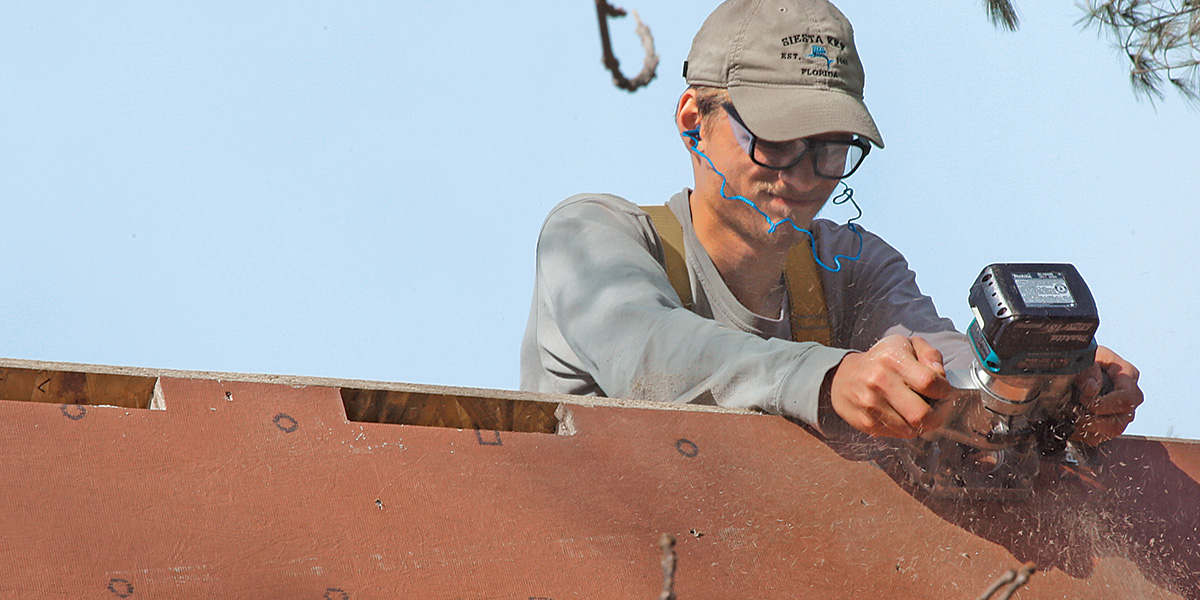
Addressing overhangs
The design called for exposed rafter tails with exposed tongue-and-groove roof sheathing that could be seen from the ground. Obviously an exposed I-joist would look bad and rot quickly. Since we had a solid LVL spanning the front of the building on the upper end of the roof and solid blocking on the lower end, we were able to build applied rafter tails to attach at these locations.
I-joist-framed roofs have some fussy details, but the long, straight engineered lumber solved a number of problems on this build. First off, I could find light, one-piece, freespan rafters, and I was able to get them onto the roof without heavy equipment. For another, they simplified the roof-venting strategy. And last but certainly not least, they were available when I needed them.
Make it air- and watertight
The taped sheathing on this house is its primary air and water barrier. Like the other walls, the eave wall is tied to the roof system for uplift resistance.
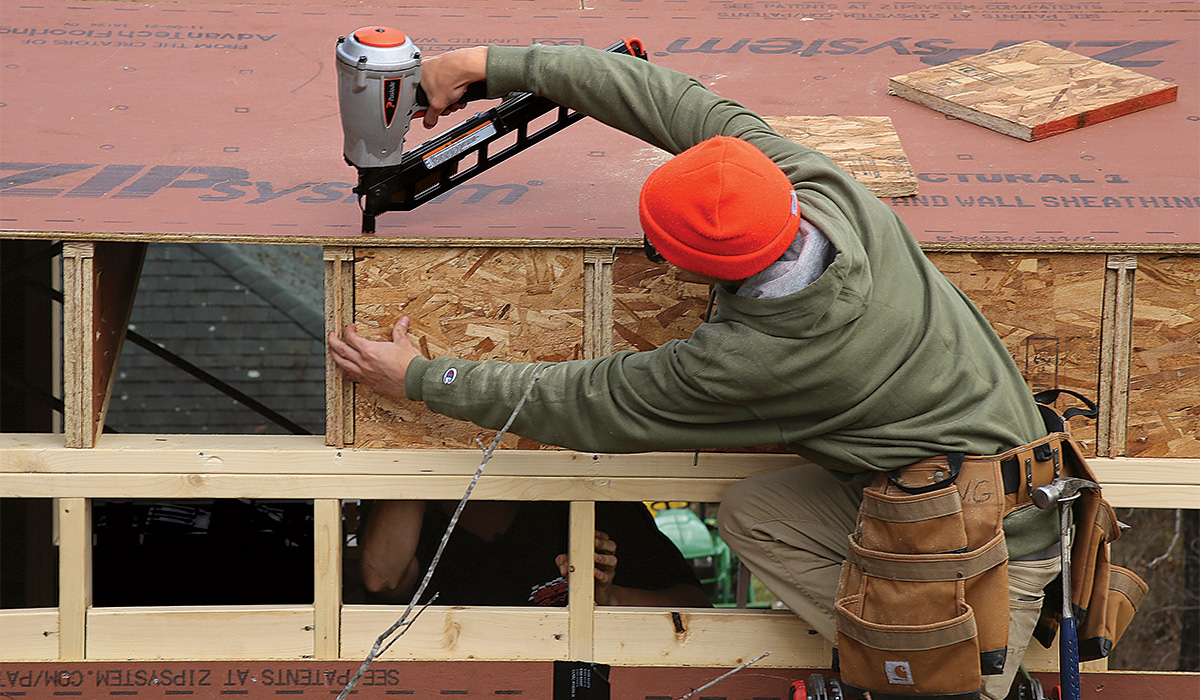
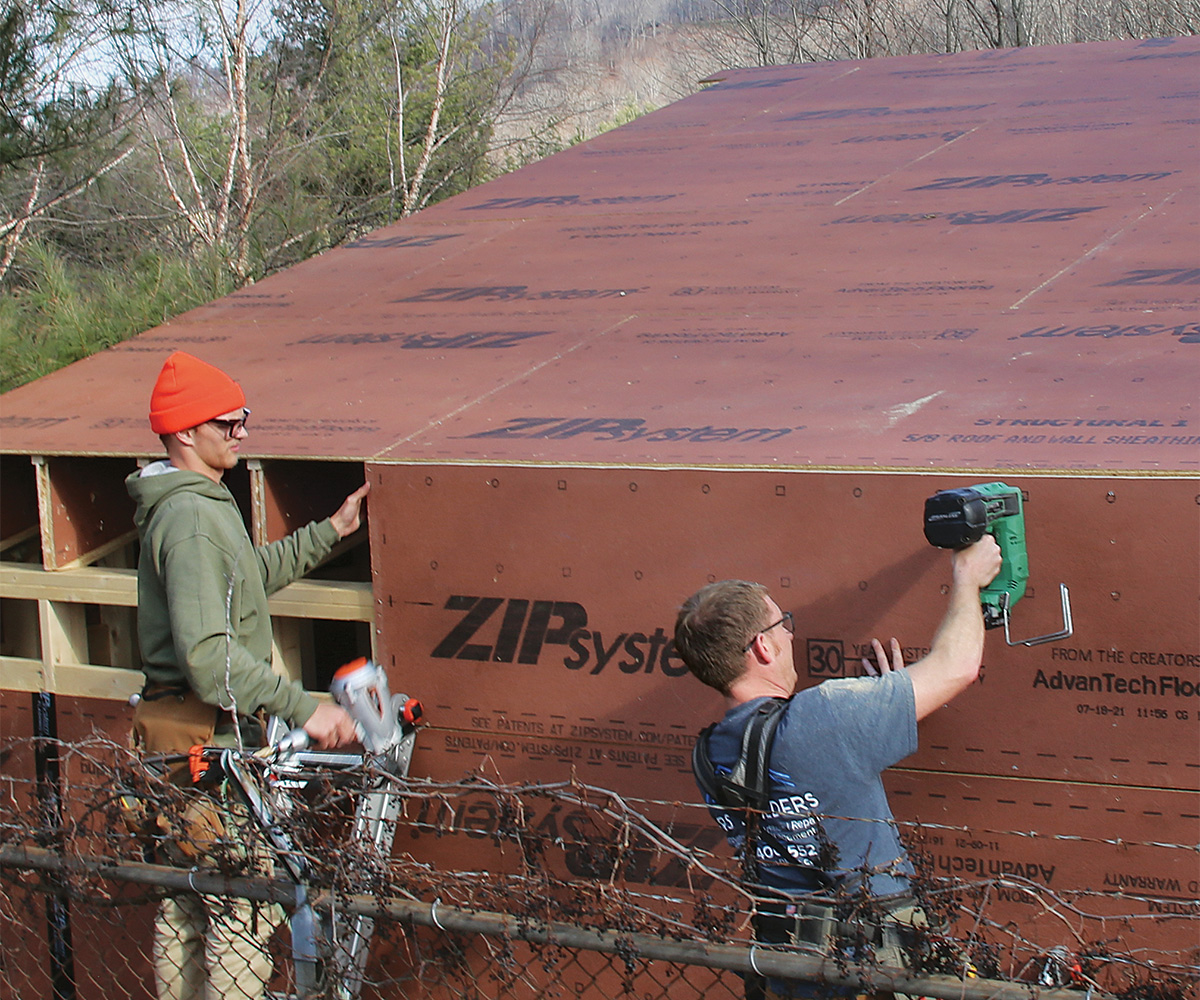
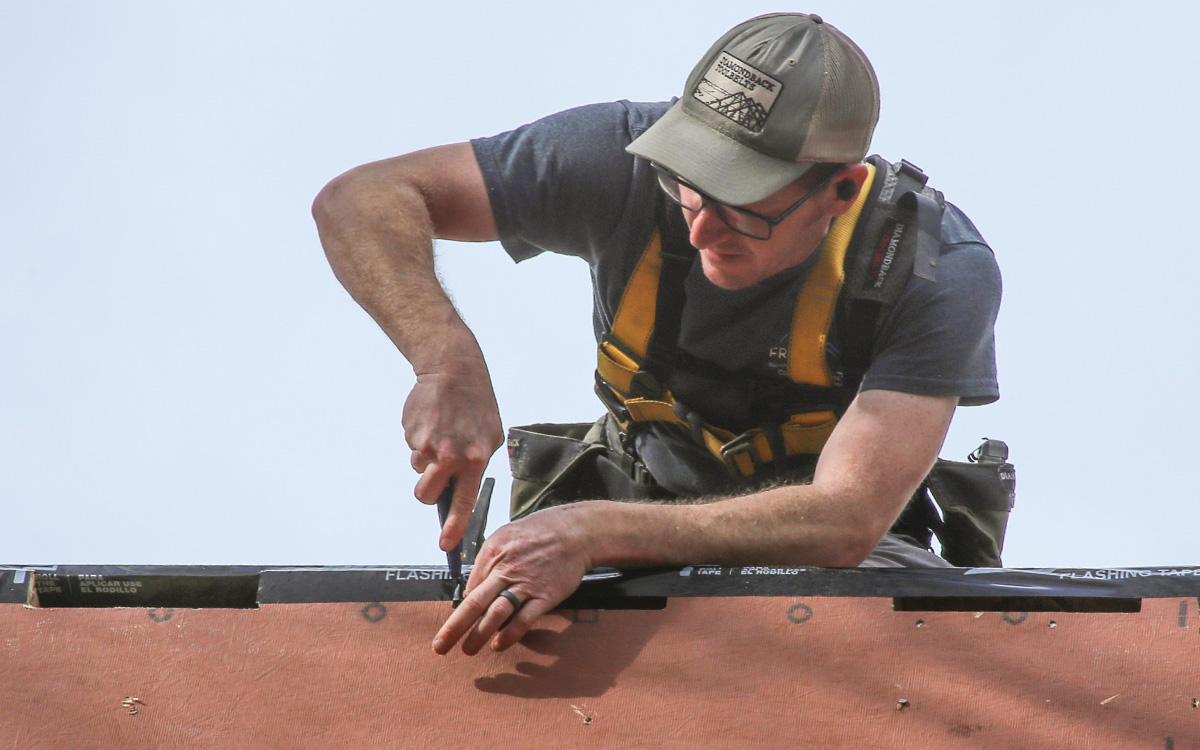
Andrew Steele is the owner of FRS Builders in Purlear, N.C.
Photos by Patrick McCombe
From Fine Homebuilding #308
RELATED STORIES
Fine Homebuilding Recommended Products
Fine Homebuilding receives a commission for items purchased through links on this site, including Amazon Associates and other affiliate advertising programs.
Stabila Extendable Plate to Plate Level
Roof Jacks
Hook Blade Roofing Knife